OUR ADVANTAGES
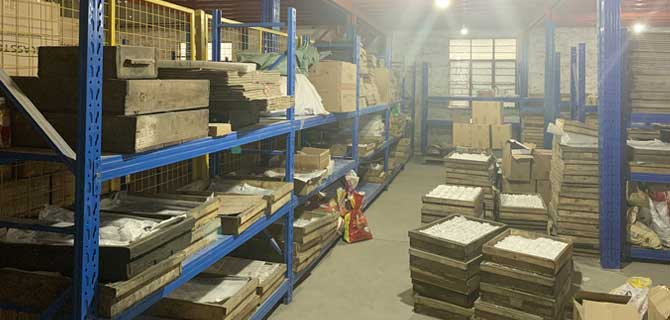
R&D
Continuous innovation, continuous breakthrough Cross the border and break the world.
Based on the introduction of new materials, new technologies, new achievements and our company’s intellectual property rights, Sateer Enterprises has established a unique R&D, production and management system. The leading products are glass door bathroom handle, glass door upper and lower clips, bathroom clips, bathroom sliding door hanging wheels, and so on. In addition, sample manufacturing and processing of special products can be provided. The company has advanced production equipment and technology, and has a group of professional teams. The annual production of products is about 1 million sets (pieces), and the Sateer enterprise has obtained the invention patent certificate and copyright certificate.Since the company’s expansion, the factory has been flooded with more powerful employees and more educated managers. The company has more than 100 employees and has introduced 30 precision CNC machine tools of better level to provide better quality products for the factory’s products.
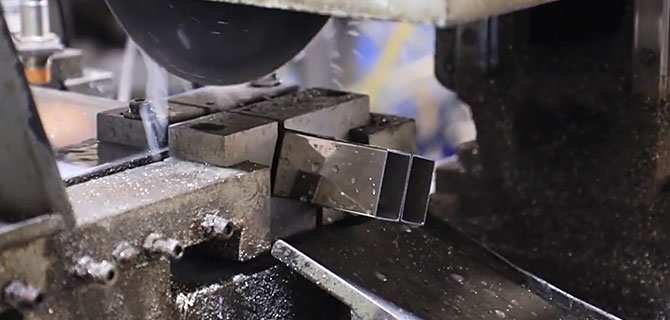
QUALITY
Work hard on quality.
Well-known domestic and imported brands, providing customers with higher specification options.
Heavy can also have quantity.
Covering all product requirements and effectively integrating for customers.
Sateer Hardware Manufacturing Co., Ltd. always regards quality as the most important thing. Only the highest quality materials are used. We also strictly monitor the entire production process and continuously improve our production technology. The highest quality standards are applied throughout the entire process, from material selection, process monitoring to pre-delivery inspection. High-quality products made from well-tested materials, and the entire production process is under very strict control, we have the best people, the latest equipment, and implement the highest standards, our hardware accessories meet industry standards and will definitely Bringing value to you with superior quality and availability, we believe in total quality, emphasizing prevention over detection. That’s why we use only the best materials and techniques to produce hardware, and our advanced manufacturing systems and skilled workforce allow us to work on your timescale to deliver the consistently high-quality hardware you expect.
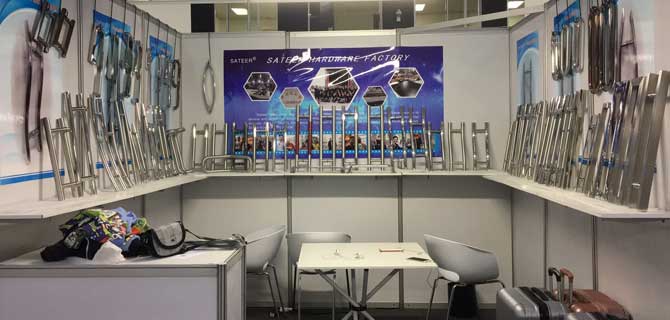
PRODUCTION
Sophisticated and detailed.
Customized services that can be processed and customized to meet customer needs in an all-round way.
Production Process:
First of all, before processing hardware compensation parts, you must clearly see the content of the process flow, clearly know the part, shape, and size of the drawings to be processed, and know the processing content of the next process. Before processing raw materials and clamping, it is necessary to measure whether the size of the blank meets the requirements of the drawing, and it must be carefully checked whether its placement is consistent with the programmed instructions. After the rough machining of the processing technology is completed, self-checking should be carried out in time, so as to adjust the data with errors in time.
The main content of self-inspection is the position and size of the processing part.
1. Whether there is looseness in the machining process of mechanical parts.
2. Whether the part processing technology is correct to touch the starting point.
3. Whether the size from the machining part of the CNC part to the reference edge (reference point) meets the requirements of the drawing.
4. The position and size of the CNC machining parts relative to each other. Measure the roughed shape ruler (except arcs) after checking the position dimensions.
Parts are finished after roughing confirmation. Before finishing, self-check the shape and size of the drawing part: check the basic length and width of the processing part of the vertical plane; measure the base point size marked on the drawing for the processing part of the inclined plane. After completing the self-inspection of the parts and confirming that they are in line with the drawings and process requirements, the workpiece can be removed and sent to the inspector for special inspection. When encountering small batch processing of precision parts, batch processing is required after the first part is confirmed to be qualified.
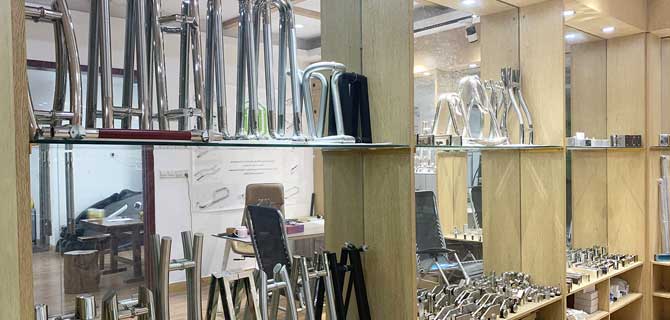
SERVICE
Service first, customer first.
1. According to customer needs, customers can carry out laser marking on conventional products, and manufacturers can also produce products and laser marking according to different requirements of customers. For example, the accessories in the handle connection can be made of iron, stainless steel, aluminum or copper. Packaging design can use standard conventional packaging or design packaging solutions provided by customers.
2. After confirming the order details, the customer sends the product logo format to the manufacturer for confirmation, and communicates to determine the logo printing position.
Assembling design drawings or documents of products and packaging that need to be sent to customers.
3. Confirm the order, after negotiating details such as product specifications, delivery date and payment terms, confirm the contract and pay the deposit.
4. Production process, make production plan to control delivery time and perform input process quality control to ensure product quality.
5. Production time, our average production lead time is 30 days.
6. Quality control, the quality team conducts OQC to ensure the quality of the finished product before allowing storage. Video and pictures of the inspection process can be recorded and sent to customers.
7. Shipment preparation, notify the customer of the shipment preparation, and the customer pays the balance. Loading photos will be taken and sent to customers.
Customs clearance documents will be issued as they become available.
8. After-sales service, if there is any problem with the product, please contact our corresponding sales staff to determine the problem and transfer it to our after-sales service department. Our technical staff will reply within 24 hours and provide guidance through photos or videos. Give a solution. If the problem is still not solved, our technicians will judge, discuss and test the solution given by the guide, and make sure that the product can be repaired and the customer can understand.